7 Best Practices to Comply With The FSMA Produce Safety Rule
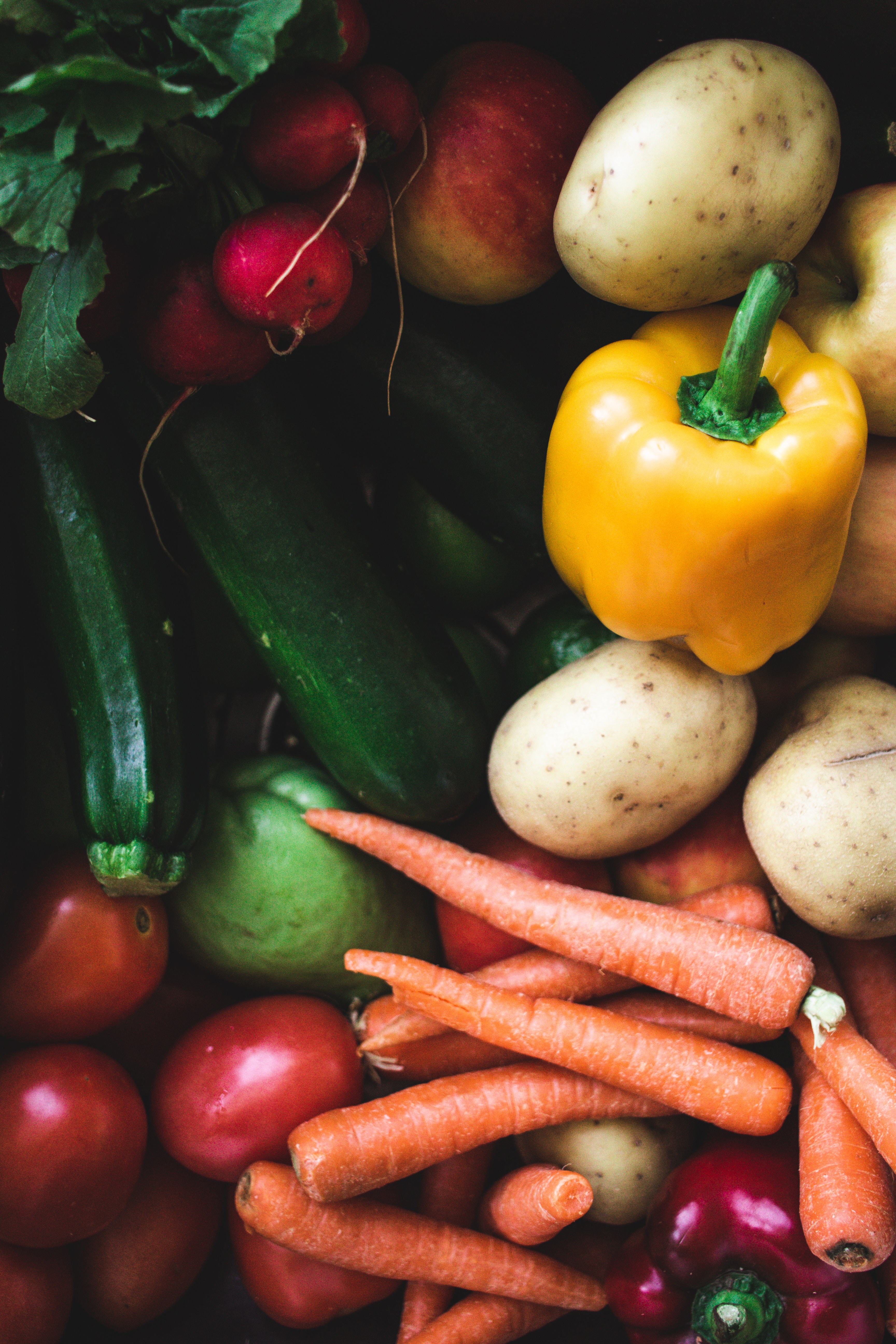
Dealing with perishables means safety and quality are paramount concerns for supply chain businesses that trade these commodities.
In this regard, adhering to the Food Safety Modernization Act’s (FSMA) Produce Safety Rule is crucial, as it outlines a federally-mandated set of standards that businesses must follow.
This blog post will discuss some of the best practices that you can implement to remain compliant. We’ll also go over how you can use Silo’s inventory management, lot tracking, and traceability features to ensure compliance.
The importance of compliance
The FSMA Produce Safety Rule is a critical piece of legislation designed by the Food and Drug Administration (FDA) to keep the food supply chain free of risk, requiring businesses that handle, store, transport, or process fruits and vegetables to adhere to standards to prevent potential product contamination.
Meeting these standards therefore becomes crucial to protect public health. For businesses, adherence protects from reputational and financial damage.
While it may seem inconvenient short term to develop and implement measures to comply with standards, doing your due diligence is important in the long run. Your business will be better equipped to handle any future incidents that may arise, and in the long-term, will increase customer loyalty, as they can trust that your products will be sourced from reliable suppliers.
7 best practices to comply with the Produce Safety Rule (FSMA)
With that said, here are some key practices that you can put in place.
1. Develop a food safety plan
A food safety plan is a document that outlines the specific steps that a business will take to reduce the risk of contamination. The plan should include key policies, procedures, and processes for managing outbreaks.
2. Conduct a hazard analysis
It’s essential to assess the risks associated with your current operations. A hazard analysis will identify and assess any potential hazards that may exist in your supply chain. This includes assessing the risk of physical, chemical, biological, or radiological contamination.
The results of your assessment will allow you to then take action to address any issues.
3. Ensure proper water quality
The Produce Safety Rule has very particular requirements for water quality, as water is used to wash down products transmitted throughout the supply chain, as well as tools and storage equipment.
Make sure to have a system in place to confirm that water quality standards are being met. This can mean taking the necessary steps to test the water used for processing before using it, depending on reliable sources of water whenever possible.
Keep detailed records of all the water tests and any corrective actions taken. Doing so will make sure you have a record of compliance in the event of an audit or inspection.
4. Make sure trade partners are using safe soil enrichments
Manure and compost are two common soil enrichments used in the production of fruits and vegetables. The FDA has very strict requirements for safely administering them, so if you work with growers, it’s crucial to know that your trade partners are handling them responsibly.
5. Ensure proper hygiene for workers handling food
Businesses should ensure that workers are practicing proper hygiene to reduce contamination risk. After outlining measures for worker hygiene (such as requiring them to wash their hands, keep clothing clean, tidy work areas, etc.), make sure you have a system in place to ensure that these necessary protocols are actually being followed.
Provide adequate training for all staff who handle food, from transport drivers to warehouse personnel. Make sure that all staff understand these protocols and address any questions they may have.
6. Maintain buildings, tools, and equipment
All buildings, tools, and equipment used in your daily operations should be maintained. This includes cleaning and sanitizing surfaces, storage spaces, and transport trucks regularly.
7. Implement a traceability system
Having a traceability system in place is essential to remaining compliant. This will help ensure that you can quickly trace the origin of any product should a recall be requested.
Many businesses have enlisted the help of technological solutions to assist with the traceability process, emphasizing easy access to actionable data.
Ensure compliance with Silo
Adhering to the FDA’s Produce Safety Rule protects consumers, customers, and businesses alike. To better comply with government regulations, consider Silo, an Enterprise Resource Planning (ERP) solution for inventory management, lot tracking, and traceability.
Businesses that use Silo benefit from centralized expense and produce tracking to enhance visibility. Not only will you be able to leverage accurate data to optimize profits, but you’ll always have a handle on available inventory. Keep an eye on products that come and go, noting important metrics like waste and profitability.
Silo’s platform provides easily accessible data so you can act quickly in the event of recalls, effectively minimizing financial and reputational damage.
Book a demo with Silo today!
Want to book a demo with us?
Add your info and we’ll get one scheduled with you.