How Inventory Management Works For The Food Industry
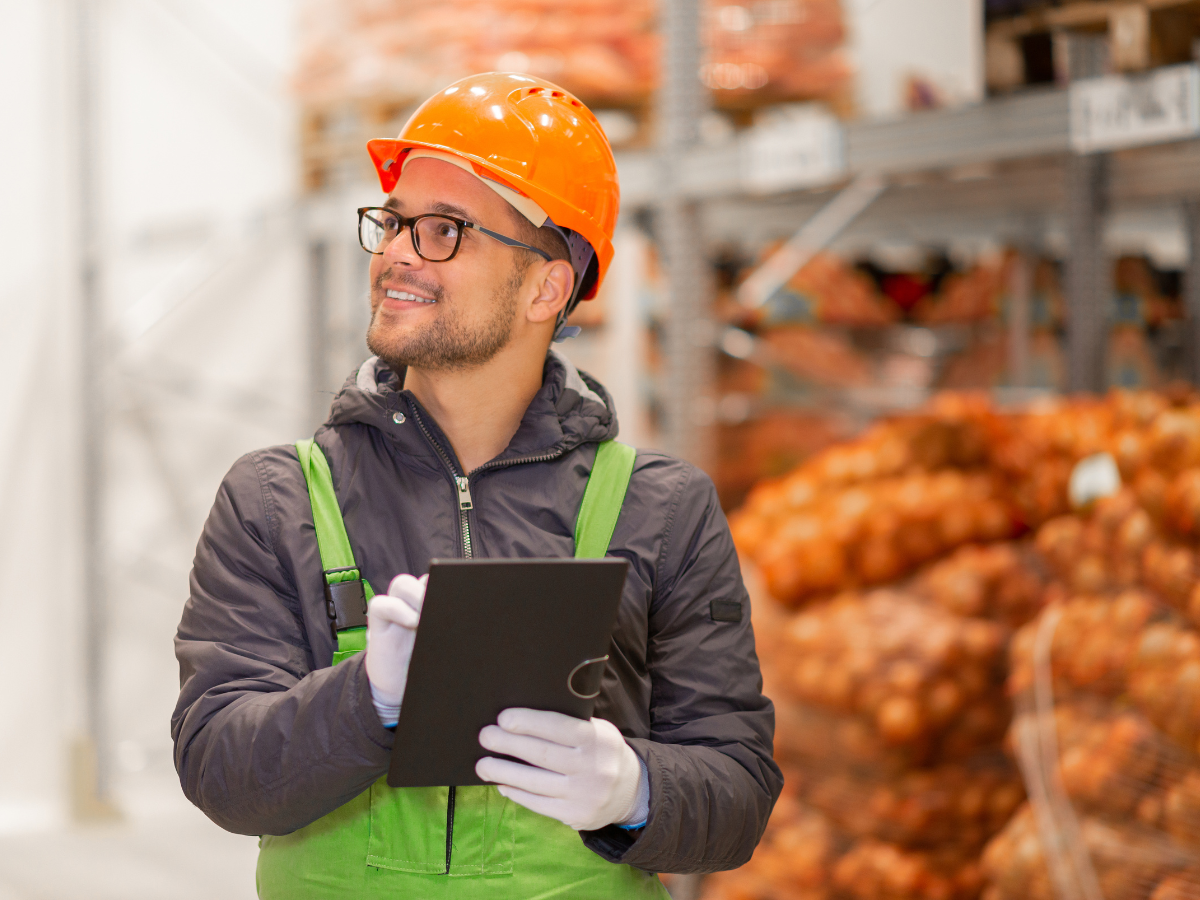
Implementing an automated inventory management system allows for the seamless transportation and processing of food products. The right solution can preserve food to help avoid spoilage and loss of profit while facilitating the fluid movement of products to guarantee on-time delivery.
Inventory management keeps track of products while providing data that can be important for determining your business’ next course of action.
Let’s go over what you need to know about inventory management and how it works. This article will provide information on the importance of this process and how an Enterprise Resource Planning (ERP) solution can help increase productivity and efficiency.
What is inventory management?
In the food industry, inventory management is the process of maintaining and monitoring food stock levels. It involves ordering, receiving, storing, and distributing food products.
It’s crucial for effective supply chain management and typically involves using a system that helps track inventory, minimize waste, and ensure that products are fresh and safely handled. Proper storage and oversight of expiration and use-by dates are essential for maintaining food quality for safe consumption, which this process can help with.
The process of inventory management in the food industry
Here’s what the inventory management process looks like.
Demand forecasting
Anticipating supply and demand helps to avoid shortages and overstocking. Demand forecasting allows businesses to make data-driven decisions about what products to order and when.
Tracking inventory
Tracking inventory accurately means monitoring product levels and identifying fast-moving and slow-moving items, which can help determine the frequency of orders. It may involve using RFID, barcoding, or manual techniques to manage customer sales and place timely orders.
Automated inventory tracking can be beneficial for adequately organizing products.
Reordering and restocking
Reordering and restocking are critical components of inventory management to ensure continuous operation without interruptions. This process not only ensures that the most popular items are always available but also minimizes the risk of excess inventory that could lead to increased waste and reduced profits.
Automated systems can establish reorder points based on historical sales data, predicting when a product’s stock will reach a critical low and trigger a replenishment order.
Quality control
Before food lands on retail store shelves and reaches consumers, it must undergo quality control inspections. Conducting adequate quality checks ensures that the food is safe to consume and is defect and damage-free.
Inventory storage
Storage is an essential part of inventory management. Different foods, especially perishable ones, must be stored, packaged, and labeled correctly. Food must be held in temperature-controlled warehouses or storage containers to avoid spoilage.
Properly organizing storage allows for quick distribution and delivery to restaurants and retail.
The role of inventory management in food safety
Created by the Federal Department of Agriculture (FDA), the Food Safety Modernization Act (FSMA) is a set of risk management regulations used to ensure the quality of America’s food supply.
At its inception, the FSMA mainly sought to respond to foodborne illnesses. Now, the legislation focuses on ways to prevent these illnesses. These changes were done so in response to the rapid globalization of the food system and the realization that preventing foodborne illness is critical for protecting public health.
The FSMA requires food companies to implement a written food safety plan and identify potential hazards in their operations. This legislation has affected the way that businesses manage their inventory, as companies must now have processes in place to monitor and prevent contamination or spoilage of products.
Inventory management, therefore, plays a crucial role in food safety by ensuring that products are properly and safely stored while also providing data to track potential hazards.
How technology helps with inventory management
Let’s discuss the advantages of using an Enterprise Resource Planning (ERP) software solution to boost the efficiency and accuracy of inventory management.
Tracking
Integrating an ERP solution into your processes can significantly improve how you track products.
An ERP platform gives employees access to a centralized database, with real-time updates and information on each product. This way, you know exactly how many orders you can fulfill and how much product to buy from a supplier.
Streamline business processes
Searching for lost inventory can waste valuable time and resources. Using an ERP system, you can easily and accurately identify products.
An ERP system also allows for the interaction of different business areas, such as sales and logistics. Inventory data helps produce trends, giving insight into customer buying habits. As a result, you can make better, more informed business decisions.
Automation
Automation eliminates the need for manual tracking, allowing your business to streamline operations to save time and money. With less manual work, employees can spend their time on more important tasks that further the success of your business.
Save money
An ERP solution minimizes labor costs, streamlines your business processes, collects factual data, tracks inventory, and builds trend reports.
This is usually done automatically and with minimal input, lowering the cost of your business’ operations. By allowing an ERP tool to do all the heavy lifting, you save money and resources while still increasing efficiency, accuracy, and precision.
Silo: the best solution for food businesses
Silo’s Enterprise Resource Planning solution combines inventory management, cash flow management, and logistics to provide real-time clarity and help your business maximize its profit.
Silo provides access to historical and market data for valuable insights. You’ll have greater confidence that you’re paying the right price for products and ordering according to the needs of customers. Plus, vendor and internal communications features help maximize performance and streamline business processes.
Silo makes purchasing products simple. Book a demo on our website to see how Silo can help you make informed business decisions and increase profit!
Want to book a demo with us?
Add your info and we’ll get one scheduled with you.